How the Concrete Industry is Combating Climate Change with China Taking the Lead
- Kendall Plein
- Jun 14, 2021
- 4 min read
Updated: Oct 4, 2021
Concrete is the highest consumed product on Earth after water. It is the most common building material, and due to the way it is produced has high carbon emissions contributing to climate change.

Concrete is responsible for at least 7% of carbon emissions and cannot be ignored by those serious about net-zero emission goals.
Relatively cheap, with a long lifespan, concrete is a staple building product. It is strong in compression, can be reinforced with steel, shaped into anything and is non-combustible. Concrete is used twice as much as any other building material like wood, steel, plastic and aluminum. Popular for its versatility and reliability, concrete is not a low-carbon building material, and so efforts are taking place to modify it and develop alternatives.
Cement is mixed with aggregate — usually stone and sand — to create concrete. This process is millennia-old, with the current standard cement using a recipe from 1824. However, some companies are testing new concrete formulas that may have lower environmental impacts. Traditional concrete is made in a reaction that creates carbon dioxide as a byproduct. 60% of concrete’s carbon emissions come from this process of mixing cement into concrete. To make carbon-neutral concrete, a new recipe for concrete must be developed.
Pressures being placed on the business world to elevate environmental standards push concrete producers to create new types of green concrete. There are a couple of strategies to accomplish this. Building with less concrete using high-strength concrete or concrete in conjunction with other building materials like wood is one strategy. In particular, cross-laminated timber, a type of mass timber, can be used in place of concrete due to its strength. High-strength concrete reduces the need for concrete in a project by 40%.
A newer strategy to reduce emissions from concrete is to create green concrete. Green concrete refers to concrete designed to have a lower environmental impact than traditional concrete. Green concrete often uses waste materials in the mix. Typical waste materials include Recycled Crushed Aggregate, Ground Granulated Blast-Furnace Slag and Pulverized Fuel Ash. These waste products are mixed into cement and reduce the need for new aggregate.
Recycled and Reduced-Carbon Concrete
Many concrete companies are looking to innovate new concrete products to help reduce emissions, with most looking to adapt the cement-aggregate recipe to lower carbon emissions.
ECOPact has the industry’s broadest range of green concrete for high performance. ECOPact uses upcycled construction materials, and its concrete is 30% to 100% less carbon-intensive than standard concrete.
[Like what you read in The Carbonic? Help support climate journalism by donating ]
Project manager Kevin Riley of Belfast Valley Contractors told ConstructionDive he didn’t “see a difference in what [ECOPact’s concrete] looks like or its set times." The firm is leading a residence hall project for Georgetown University in Washington, D.C., using ECOPact’s concrete. The more construction crews, architects and engineers feel comfortable with green concrete, the more green concrete will become the norm.
CarbonCure is another company trying to reduce carbon emissions from concrete. CarbonCure injects carbon dioxide into concrete in a process called CO2 mineralization. The company claims CO2 mineralization improves concrete's performance and strength. CarbonCure's concrete product, installed in 60 Irving Materials, Inc. carbon plants, has saved 37.5 million pounds of carbon emissions.
Another company pushing the concrete needle, BluePlanet, Ltd. uses sequestered carbon to create aggregates for green concrete. Their CO2-sequestered aggregate contains 440 kilograms of carbon dioxide per ton of aggregate. BluePlanet also offers upcycled aggregate made from demolition waste.
All these companies are innovating new products, but they are not yet the norm. The construction industry still has a long way until low-carbon concrete reaches market saturation.
Trends in the Concrete Industry
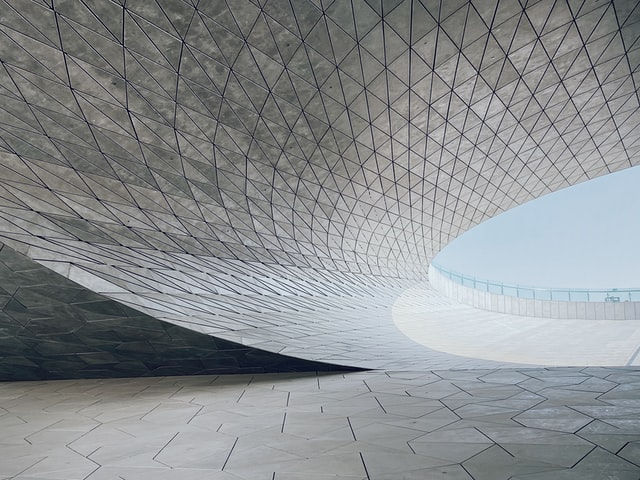
Emissions from concrete have decreased about 25% per ton since 1990, but this was the easiest 25%, Ian Riley, CEO of the World Cement Association told BloombergNEF. Riley says the industry now has to look to new technologies, which take longer to gain acceptance. Concrete as a building material must go through rigorous testing for safety and strength, which slows innovation.
The Global Cement and Concrete Association drives “advances in sustainable construction while demonstrating sustainable industrial leadership in cement and concrete manufacturing." GCCA encompasses 30% of total cement production, and through Sustainability Guidelines, is trying to push the industry towards carbon neutrality.
HeidelbergCement, the second-largest cement producer globally, has pledged to make their Swedish factory carbon neutral. This would be the first carbon-neutral cement plant in the world. HeidelbergCement plans to capture 1.8 million tonnes of carbon dioxide per year to offset emissions. However, there is no indication that HeidelbergCement will reduce emissions by producing green concrete. Instead, HeidelbergCement will rely on offsetting its emissions. This strategy may not be scalable, as the entire cement industry emits over 4 billion tonnes of carbon dioxide a year.
Political Pressure Slow to Build
Concrete and building emissions are often ignored in environmental policy. There has been some political pressure to reduce carbon emissions, but no one is driving the change as hard as needed. Most of the innovation for green concrete comes from the market, not any governing bodies.
Europe has a carbon-trading scheme that includes the cement industry. However, the system unintentionally benefitted the cement industry rather than the planet. European cement plants were able to meet the quota set by the EU trading scheme because they ran all their plants at 51% rather than close down inefficient plants, Bloomberg NEF reported.
China has stricter standards for new concrete plants. There are standards for energy usage, with gradually increased penalties. China also mandates waste-heat power generation. Cement plants in the U.S. and Europe are quite old and were built under older standards. These plants would not be able to run in China due to their inefficiencies.
The U.S. is not prioritizing green concrete at the level of other countries. The Biden Administration has focused on renewable energy and electric vehicles to lower emissions, while concrete and the construction industry is largely ignored. Globally, the construction industry accounts for 40% of carbon emissions. Construction and urbanization are ever-increasing, and the construction industry must adapt to cut greenhouse emissions.
Concrete is one of the most essential materials to modern humanity. However, it goes unnoticed by many climate initiatives. Although cutting carbon emissions from the construction industry is more difficult than electrifying transportation, innovative concrete companies are working to create low-carbon concrete. However, the industry standard relies on old technology that emits more carbon than acceptable.
Drop a line to contact@thecarbonic.com for newsletter subscriptions, tips, questions or comments.
Comments